One of the big questions people ask when starting a building project in Nigeria is “Should I buy blocks from a supplier, or should I mould them on-site?”
At first glance, buying blocks seems easier just pay and they’re delivered.
But moulding on-site gives you control over quality and cost.
So which one is actually better?
In this article, Bullionrise consult will break down the pros and cons of both options, so you can make the best decision for your project, budget, and location.
Table of Contents
ToggleSee related – How to check the quality of blocks before buying
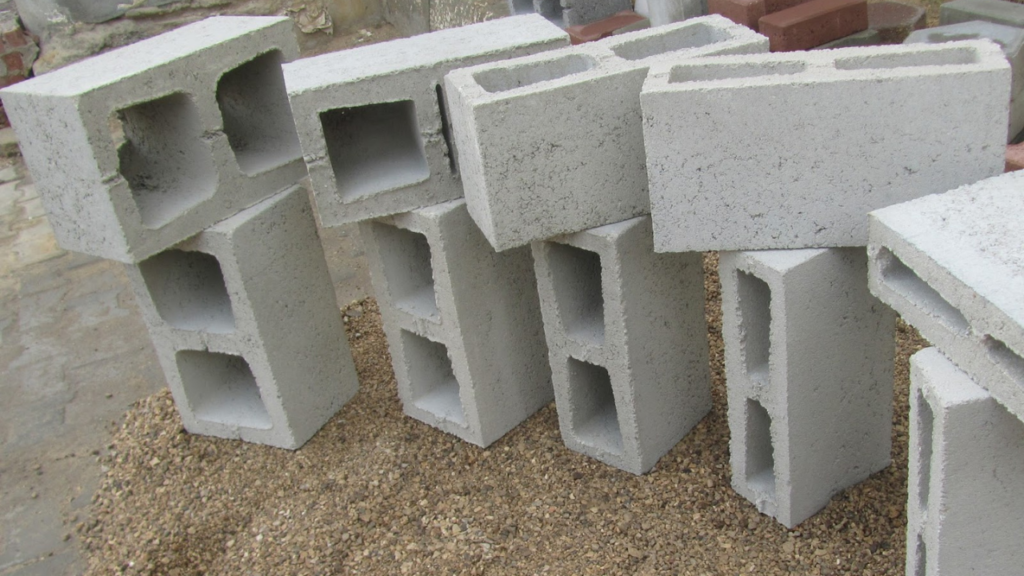
Buying Blocks From Suppliers
Pros (Advantages)
1. Convenient and Fast
You don’t need to wait for blocks to be moulded and cured, just buy and build.
2. Saves Labor and Space
No need to hire laborers for block production or worry about curing space on-site.
3. Available in Bulk
Big suppliers have machines that produce thousands of blocks daily which are useful for large projects.
4. Reduces Project Delay
Speeds up construction, especially in urgent projects.
Cons (Disadvantages)
1. Uncertain Quality
Many block makers use poor cement-sand ratios (1:10 or worse) to cut costs, leading to weak blocks.
2. Higher Cost per Block
You pay more because the seller adds profit margin, transport, and overhead costs.
3. Risk of Damage in Transit
Blocks may break or chip before getting to your site, especially over long distances.
See also – Which block is best for foundation | how to figure it out
Molding Blocks On-Site
Pros (Advantages)
1. Control Over Quality
You can ensure the right cement-sand ratio (like 1:6), use sharp sand, and ensure proper curing.
2. Cost-Effective
While it involves labor, it’s often cheaper than buying especially for big projects.
3. Reduces Waste and Breakage
Since blocks are not transported, the chances of damage are low.
4. Custom Sizes and Mixes
You can mold different block sizes (9-inch, 6-inch, solid, etc.) based on your project needs.
Cons (Disadvantages)
1. Takes Time
Molding and curing blocks takes time, ideally 7 days minimum before use.
2. Needs Space
You need enough land to mold, stack, and cure the blocks properly.
3. Requires Supervision
If you’re not careful, your laborers may use poor mix ratios or water down the cement.
4. Extra Labor and Logistics
You’ll have to manage workers, water supply, materials, and curing adds to site stress.
See also – Which is better, hollow blocks or solid blocks?
So, Which Is Better?
- For Small project or urgent timeline, Buy blocks.
- For Large project with time & space, Mold on-site.
- If you Want control over quality, Mold on-site.
- For Remote area with no good suppliers, Mold on-site.
- For Urban area with trusted suppliers, Buy blocks.
- For Limited land space, Buy blocks.
You can use both options in stages:
- Start with bought blocks for foundation work (if urgent).
- Then mold the rest on-site while other work is ongoing — especially if you’re building in phases.
See also – Which block is best for foundation | how to figure it out
Conclusion
There’s no one-size-fits-all answer. The best choice depends on your budget, quality concerns, space, and project timeline.
If you want top-notch quality and are willing to manage the process, molding on-site is better.
But if you want speed and convenience, buying blocks may save you stress.
Either way, never compromise on block quality, the strength of your building depends on it.
Frequently asked questions
Which is more cost-effective: buying blocks or molding on-site?
- Buying blocks can be more expensive upfront because manufacturers factor in labor, transportation, and profit margins.
- Molding on-site can reduce costs, especially for large projects, by eliminating transportation fees and allowing control over material usage. However, labor and equipment costs must be considered.
Does molding blocks on-site ensure better quality compared to buying?
- On-site molding allows direct control over the mix ratio, curing process, and material selection, ensuring higher quality.
- Pre-made blocks vary in quality based on the manufacturer. Reputable suppliers ensure consistent strength and durability, but lower-quality blocks may be weaker due to improper mixing or curing.
What are the advantages of buying pre-made blocks from a manufacturer?
- Saves time and effort by eliminating on-site production.
- Ensures uniform size, strength, and quality if sourced from a reputable supplier.
- Reduces labor costs and the need for specialized block-making equipment.
- More convenient for smaller projects or sites with limited space.
What challenges come with molding blocks on-site?
- Requires space for mixing, molding, and curing.
- Needs skilled labor to ensure proper mix and uniform blocks.
- Weather conditions can affect block curing, leading to weaker structures.
- Initial setup for molds and equipment can add to costs.
How does the availability of materials affect the decision to buy or mold blocks?
- If high-quality sand and cement are readily available, molding on-site can be a cost-effective option.
- In areas where raw materials are scarce or expensive, buying pre-made blocks may be more practical.