In Nigeria, blocks are the backbone of most buildings, from residential homes to commercial structures.
But not all blocks are created equal.
Some are well-made and durable, while others are poorly mixed, easily breakable, and dangerous to use for construction.
If you’re building a house, school, shop, or even a fence, it’s crucial to check the quality of blocks before buying.
Using low-quality blocks can lead to cracks, water seepage, and even building collapse.
In this article, Bullionrise consult will show you simple but effective ways to test block quality even if you’re not an engineer.
Table of Contents
ToggleSee also – Which block is best for foundation | how to figure it out
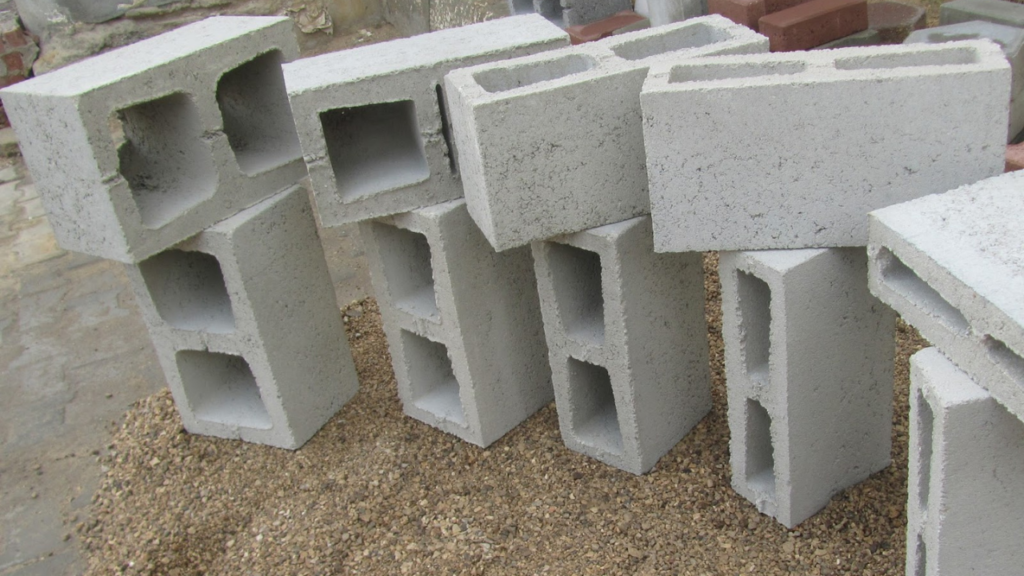
Why Block Quality Matters
- Structural strength: Good blocks support the weight of the building.
- Durability: High-quality blocks last longer and resist harsh weather.
- Safety: Weak blocks can cause wall cracks or collapse.
- Cost-saving: Using poor blocks leads to repairs or rebuilding, which costs more in the long run.
Types of Blocks Commonly Used in Nigeria
- 9-inch hollow blocks – used for external and load-bearing walls.
- 6-inch hollow blocks – used for internal partition walls.
- Solid blocks – used for foundations or walls requiring extra strength.
Regardless of type, the quality of the block matters.
See related – Which is better: buying blocks or molding on-site
How to Check the Quality of Blocks Before Buying
1. Visual Inspection
Look at the block closely. Good quality blocks should:
- Have sharp edges and uniform shape
- Be well-compacted and smooth on the surface
- Be free from visible cracks or holes
- Show no signs of excessive sand or powdery surfaces
Blocks that are rough, cracked, or crumbling on the edges are likely poor quality.
2. Weight Test
Lift a block and feel its weight:
- Heavier blocks are usually better, they contain more cement and less sand.
- Light or hollow-feeling blocks may have too much sand or poor mix ratios.
But be cautious some block makers may use gravel or laterite to make blocks feel heavy without being strong.
3. Sound Test (Ring Test)
Gently knock two blocks together:
- A high-pitched ringing sound indicates strength and proper curing.
- A dull or thudding sound often means weak or poorly cured blocks.
This is one of the fastest and easiest on-site tests.
4. Drop Test
Drop the block from waist or shoulder height (about 1 meter):
- A good block should remain intact or have minimal chipping.
- If it breaks or crumbles easily, avoid buying.
Note: Don’t overdo this, use 1–2 blocks as samples, not all.
5. Water Absorption Test
- Soak a block in water for about 10–15 minutes.
- If the block absorbs too much water, it’s made with too little cement.
- A quality block should resist water and not become soft or disintegrate.
This test helps determine durability and suitability for wet environments.
6. Ask About the Mix Ratio
Block makers should be able to tell you the cement-to-sand ratio used.
- A good mix is usually 1:6 (1 bag of cement to 6 head pans of sand) or better.
- Ratios like 1:8 or 1:10 are poor and produce weak blocks.
If they’re not sure of their ratio that’s a red flag.
7. Check the Curing Time
Ask when the blocks were made. Concrete blocks need at least 7 days of curing (kept moist and shaded) to gain strength.
Fresh blocks that haven’t cured properly will be weak and should not be used yet.
See also – What is sandcrete blocks, uses and advantages
Bonus Tips from bullionrise consult
- Buy from trusted or certified suppliers.
- Ask for samples before making a bulk purchase.
- Consider producing your own blocks on-site if you want full control over quality.
- If you’re building a major structure (like a duplex or storey building), get an engineer to inspect the blocks before use.
Conclusion
Checking the quality of blocks before buying is one of the smartest decisions you can make when building in Nigeria.
Even if you’re not an expert, these simple tests visual check, weight test, sound test, drop test, water test, and asking questions can help you avoid costly mistakes.
Remember, a building is only as strong as the blocks it’s built with. Don’t cut corners build with quality or don’t build at all.
Frequently asked question
What visual signs indicate a high-quality block?
A good-quality block should have a uniform shape, sharp edges, and a smooth surface.
It should be free from cracks, holes, or excessive roughness.
Color consistency can also indicate proper mixing and curing.
How can I test the strength of a block before purchasing?
You can conduct a simple drop test by dropping a block from waist height onto a hard surface.
A high-quality block should remain intact or break into large pieces rather than crumbling.
For a precise test, laboratory compression tests measure the actual strength.
What is the water absorption test, and why is it important?
The water absorption test checks how much water a block retains, which affects durability.
A good-quality block should absorb less than 12% of its weight in water.
To test, weigh a dry block, immerse it in water for 24 hours, and weigh it again.
The difference should be minimal.
How does the density of a block affect its durability?
Higher-density blocks are stronger and more durable, making them suitable for load-bearing walls.
Blocks with excessive air pockets or lightweight composition may be weaker and unsuitable for structural use.
Are there specific standards or certifications for block quality?
Yes, blocks should meet industry standards such as NIS (Nigerian Industrial Standards) or ASTM International Standards.
These regulations ensure minimum strength, curing time, and quality for construction safety.